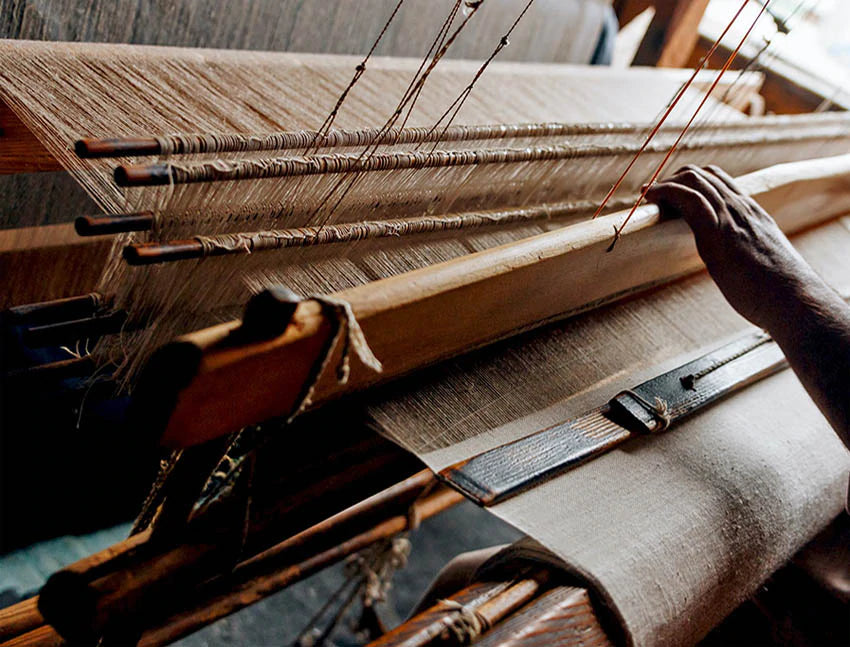
Making Our Felted Cashmere Scarves: The Process
What if we say you could trade your chunky mufflers or thick scarves on chilly winters for something light and wispy yet no less effective? You’ll probably think we’re crazy. But the truth is, it can be done with an organic fabric that goats swear by!
At Felted Cashmere, we offer lightweight scarves woven on traditional looms. Each 200/2 scarf is made with pure cashmere fibers of 14 to 16 microns and 25 to 50 mm long. Hand-felted, the cashmere scarf has a soft and delicate look with an incredibly strong and well-made feel to it.
Today, we’ll let you in on our wonderful product, how it’s made, and why they’re worth the investment.
So, what is cashmere? And where do we source it from?
Cashmere, one of the lushest and softest forms of wool, comes from the hair of cashmere goats or pashmina goats. At Felted Cashmere, ours are sourced from the Chyangra Cashmere, an exclusive breed of goats living in Nepal's snowy valleys of the Himalayas.
With their protective two-layer coat, Chyangra Cashmere goats fight off the harsh winters (that can go as low as -40℃) in altitudes of more than 4,000 meters above sea level. Their double-fleeced coating combines a rough, thick outer layer and a fine, downy undercoat.

Now, how do we process the cashmere fibers into felted cashmere scarves?
Cashmere scarves are undeniably elegant. But much work has to be done to convert cashmere fibers into fine, soft, and sheer scarves. All thanks to the masterful hands of the native Himalayan artisans, we can share in their heritage and indulge in such luxurious products.
The meticulous process involves:
- Timing the harvest – Waiting for the right time to collect the best cashmere fiber
The finest cashmere fibers are obtained during the molting period, when a cashmere goat sheds its hair coating. This natural process takes place in spring, which starts in the last days of March and ends in the early days of May. With the end of the freezing winters, the goat welcomes the warmer temperatures by shedding its hair.
Great care and precision are required to sort through thick coarse hair and fine, downy ones. The thick ones found on the back of the goats are rough and rugged because they are more exposed to the outer environment. These are about 2 to 8 inches long and more than 30 microns thick. On the other hand, fine hairs are found on the underbelly and below the throat area. These are 1 to 2.25 inches long and 14 to 16 microns thick.
- Combing – The gentle process of obtaining the finest cashmere hair
To obtain the best quality of fibers, cashmere goats are hand-stroked and combed using a special brush. The teeth of these brushes are specially designed to separate the finest fluff off the coarse hair. For a single goat, the process takes about 1 to 2 hours and yields only 150 to 200 grams of cashmere wool in a year.
The limited yield makes cashmere a prized commodity. As such, products made from it are viewed as thoughtful investment pieces.
- Dehairing – Refining the collected cashmere wool

- Spinning – Turning delicate cashmere fibers into strong yarns
On a spinning wheel called charkha, the fibers 25 to 50 mm long are gathered and spun into yarn by the talented women of Nepal.
There’s a simple rule to the quality of cashmere yarn: "The longer the fiber, the more perfect the yarn will be." Lengthier fibers come out more compact when intertwined. These make for strands that are stronger and less prone to pilling.
- Weaving – The part where the magic happens
Like generations before her, a Nepalese weaver carries out the weaving on a traditional handloom. She starts with setting up the warp (vertical strands), which determines the length of the final woven piece. After passing the hank yarn through a maze of loom parts, the warp is ready to receive the weft yarn (horizontal thread).
The master artisan winds the weft yarn on a bobbin with a charkha. Next, the weft yarn, which forms the width of the final woven piece, is shuttled to and fro, smoothly going over and under the warp threads. With this rhythmic dance between warp and weft yarns, a fabric slowly builds itself behind the careful attention of the master artisan.
Weaving the cashmere scarf on a traditional handloom
- Dyeing – Tinting the cashmere scarf in your favorite color
After the woven scarf has dried, it is hand-dyed into the desired color. Our native dyers use vegetable dyes in the process.
To date, our scarves come in 47 solid colors.
- Felting – Taking an extra step for our cashmere scarves
Hand-felting the cashmere scarf using an alkaline solution
Checking the progress of the hand-felting on the cashmere scarf
At Felted Cashmere, we do the felting entirely by hand, exercising extreme care throughout the process. The cashmere scarf is immersed in an alkaline solution and rubbed vigorously until the interlocking structure you see fresh out of the loom becomes less defined and fuzzy. By then, the scarf should feel firmer and sturdier.
After the felting process, the scarf is laid flat on a surface or hung to dry at room temperature for 2 to 4 hours.
A close-up look of the cashmere scarf after the hand-felting process
…And that explains the process of making our felted cashmere scarves.
What makes our featherlight felted scarves so special?
Having perfected the knowledge passed on from generations and honed their art through experience, master artisans from Nepal execute every step with utmost precision and mastery.
The weavers humbly carry out the processes, from harvesting the hair, spinning the yarns, weaving the fabric, and dyeing the scarves. And for cloud-soft and pilling-resistant weaves straight out of the box, they take the process further by hand-felting them.
This community effort brings us sheer, soft, and light-as-air cashmere scarves and whole stories of master artisans in the Himalayas.
See and feel our felted cashmere scarves' beauty, softness, strength, and soul.